Planetensingel Alphen aan den Rijn
door P. Engels
Wie het kleine niet eert…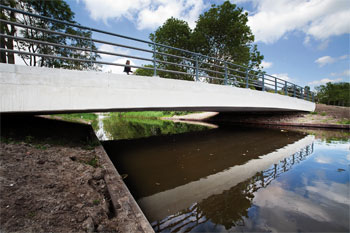
De brug in de Planetensingel in een woonwijk in Alphen aan den Rijn, zou aanvankelijk als een in het werk gestorte betonbrug worden uitgevoerd. Maar dat veranderde toen Van Hattum en Blankevoort Regio Zuid bij Spanbeton te rade ging. De brug kon evengoed in prefab beton worden gemaakt en dat pakte goedkoper uit. Er werden enkele concessies in het uiterlijk gedaan, maar één uitgangspunt bleef onwrikbaar: de brug zou een overspanning van 20 meter krijgen in een verticale boogvorm, zodat mensen in roeibootjes er ongehinderd onderdoor konden varen.
De prefab oplossing voorzag in negen getoogde
R-balken, elk 990 mm breed en 520 mm hoog, met daarop een in het werk gestort dek van gewapend beton, dik 180 mm. De liggers zijn zo ontworpen dat ze in het midden van de overspanning een verticale boog hebben van 280 mm. Niettemin lopen de voorspanstrengen gewoon in een rechte lijn van kop tot kop. In maart 2010 zijn de liggers gemonteerd.
Speciale afwerking wegdek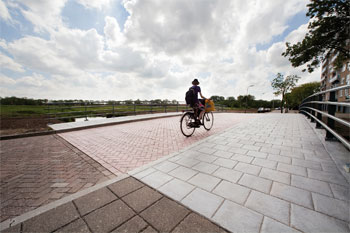
Bijzonder zijn de afwerking van het wegdek en het trottoir van de brug. Hierbij is Creteprint toegepast, waarmee in het verse betonoppervlak een gepaald patroon wordt gedrukt. Voorafgaand is in poedervorm een kleurstof gestrooid en ingeschuurd. Daarna werd met speciale mallen de structuur van een klinkerwegdek en trottoirtegels aangebracht. De bewerking wordt afgerond met het aanbrengen van een coating, die de kleurslijtlaag beschermt tegen uitdrogen en een hoge slijtvastheid oplevert.
Hiermee is aangetoond dat ook voor kleine projecten een uitvoering in prefab beton zeker mogelijk is.
Elkaar inspireren bij moderne bruggenbouw
door P. Engels
Samenwerken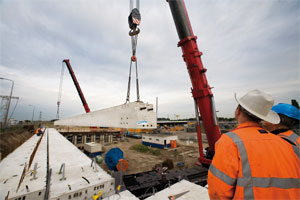
Voor een producent van betonnen brugliggers is samenwerking met een specialist op het gebied van voorspannen zo niet een vereiste, dan toch wel een verstandige zet. Er ontstaat bovendien een wederzijdse beïnvloeding. Spanbeton werkt samen met Dywidag-Systems International (DSI) uit Zaltbommel. Ing. Sander van Ameijde van DSI zegt daarover: “Zonder ingenieuze voorspantechnieken geen slimme betonliggers. En: zonder complexe vraagstukken in de bruggenbouw geen geavanceerde techniek”. Door de krachten met andere bedrijven te bundelen, ontstaat een ‘goed span’. Op die manier kun je met relatief ‘eenvoudige’ liggers een slimme constructie te maken. Want die slimheid wordt meer en meer gevraagd bij bruggen en viaducten. Dat hangt samen met het complexer worden van de constructies, slanker, groter, duurzamer, efficiënter en - als het even kan – moet er sneller gebouwd worden.”
Hoe stimuleer je elkaar om grenzen te verleggen? “Dat is een vraag die niet alleen bij speciale gelegenheden mag opkomen. Het moet eigenlijk de filosofie van een kwaliteitsspeler bepalen”, vindt Sander van Ameijde. ”Je zult regelmatig bij elkaar over de vloer moeten komen en tijd in elkaars doen en laten steken. Alleen op die manier kom je tot een ontwerp, constructie of uitvoeringstechniek van een brug of viaduct die specifieke oplossingen aandraagt voor een volgend project. Het is overigens niet alleen vooruit kijken. Als Dywidag evalueren wij ook gerealiseerde projecten, samen met andere partijen, omdat daar veel van te leren valt.”Naast kennis is ook een zekere mate van eigenwijsheid en durf nodig om iets nieuws voor te stellen. Van Ameijde: “Durf buiten gebaande paden te treden. Zeker als je met een partij als Rijkswaterstaat te maken hebt, die daar voor openstaat. Met het 3P-liggersysteem van Spanbeton is een klapper gemaakt. Het was vooraf een grote gok om van losse elementen één systeem te maken. In het geval van het viaduct over de A2 bij Breukelen (het eerste project met het 3P systeem) moest van kokerliggers een samenhangende constructie worden gemaakt op basis van voorspantechnieken in drie richtingen. Zo ontstond een brugdek dat voldeed aan de normeisen. De voorspantechniek speelt daarin een grote rol, niet alleen technisch, ook economisch. Spanbeton is er samen met DSI in geslaagd om een brugsysteem te ontwikkelen waarbij we zo’n 20 cm hoogtebeperking winnen op een overspanning van 50 m. Dit betekende een forse stap vooruit voor prefab brugdelen, mede gelet op wensen van de architecten die een voorkeur hebben voor slanke brugprofielen. En als je eenmaal een vernuftig systeem hebt, dan zul je dat verder moeten ontwikkelen om steeds een stapje vooruit te komen. Zo is het 3P-systeem verder verbeterd in een 4P-systeem, waarbij dankzij dwarsvoorspanning ter plaatse van de kopeinden van de liggers de traditionele en soms hinderlijke oplegbalk kon worden weggelaten. Hiermee kon in het project van de brug over de Zuid-Willemsvaart de architectonische wens worden gehonoreerd om zichtbare opleggingen van de balken te voorkomen.”
‘Knutselen’
Natuurlijk zit er een spanningsveld tussen dergelijke innovaties enerzijds en de druk van de markt en het tijdsaspect anderzijds. “Innovatieve technieken krijgen te weinig kans; men maakt de brug liever 10% dikker. Toch zijn er gelukkig technici die bij een offerteaanvraag niet meteen met de standaardoplossing aankomen, maar het aantrekkelijk vinden aan een ontwerp te ‘knutselen’ om met een slimmere oplossing te komen. De bruggenbouw blijft mensenwerk en mensen kunnen oplossingen tegen het licht houden en kijken of ze beter, mooier en goedkoper kunnen bouwen. Neem een ontwikkeling als de spankar, destijds bedacht voor het Boogviaduct van de Ringlijn. Wat veiligheid en arbeidsomstandigheden betreft, een prima voorziening in de moderne bruggenbouw.”
Blijven ontwikkelen en innoveren. Het is van groot belang voor de Nederlandse bruggen. Sander van Ameijde besluit: “Kijk maar eens naar de behoefte om bestaande bruggen te versterken en uit te breiden, omdat respectievelijk de verkeerslasten en verkeersdruk toenemen. Dat biedt kansen voor prefab betonliggers in combinatie met voorspanning. Bij bestaande stalen bruggen moeten soms rigoureuze ingrepen gebeuren, terwijl bij veel betonnen bruggen nog een reservecapaciteit aan draagkracht in de betonconstructie aanwezig is, zo is mijn ervaring. Dan kun je gemakkelijker een constructie versterken en verbreden. Er kan veel met spantechnieken.”
Nog even de brug over de Zuid-Willemsvaart
In een eerdere uitgave van BRUGGEN is aandacht aandeze brug in ‘s-Hertogenbosch besteed (jaargang 17 nr. 1, maart 2009). Eén facet uit dat artikel benadrukt de samenhang tussen prefab en voorspanning.
Hoewel het overspanningenschema (50 – 53 – 35 m) niet voldeed aan het ideale schema waarbij de lengte van de middenoverspanning 1,2 x de lengte van de eindoverspanning bedraagt, bleek het toch mogelijk om de brug te realiseren met een constructiehoogte van slechts 1,50 m. Voor een deel was dit te danken aan de kruisingshoek van 69º van het brugdek (de hoek tussen de lengteas van het brugdek en de as van de landhoofden en pijlers). Bij een scheve kruising kan een torsiestijve constructie namelijk een iets kortere draagrichting aannemen.
Een andere ontwerpuitdaging was het vinden van een oplossing voor een draagconstructie voor een Spanbeton 3P liggersysteem zonder onderslagbalken en met bij voorkeur een korte bouwtijd. Omdat de liggers ter plaatse van de middensteunpunten nagenoeg kop aan kop werden geplaatst was de toepassing van een brede natte knoopverbinding geen optie. Daarom is, evenals bij het Spanbeton 3P systeem een oplossing gezocht die gekenmerkt wordt door een maximale uitnutting van hoogwaardige beton en voorspanning. Het hoogwaardige beton is beschikbaar in de massieve einden van de kokerliggers en door de voegen tussen de liggereinden lokaal over de gehele hoogte te vullen en voor te spannen, wordt als het ware een inwendige pijlerbalk verkregen die de oplegkrachten over de kolommen kan verdelen.
Zo is het Spanbeton 4P systeem ontstaan waarbij het brugdek rust op cirkelvormige kolommen met een onderlinge afstand van 3,0 m, gemeten haaks op de brugas.
Marinus van Tyrusviaduct
door P. Engels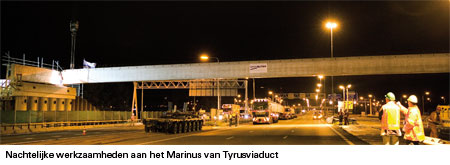
Aantrekkelijke mix van architectuur en techniek
Het Marinus van Tyrusviaduct over de A2, onderdeel van het project Hooggelegen, zorgt voor een verbinding tussen de Utrechtse kantorenwijk Papendorp en de nieuwe Stadsbaan, met aansluitingen op de A2, De Meern en Leidsche Rijn. Waar andere viaducten rond Hooggelegen uit de koker van Rijkswaterstaat voortkomen, is bij dit project de gemeente Utrecht leidend, ook qua architectonische uitstraling van dit viaduct. Als resultaat is een aantrekkelijke mix ontstaan tussen de vormgevingswensen van de opdrachtgevende partijen en tussen deze architectonische wensen en de techniek.
Ir. Paul Scheublin, projectmanager infrastructuur van het Projectbureau Leidsche Rijn gemeente Utrecht, beschrijft de stedenbouwkundige en architectonische uitgangspunten: “De verbreding van de A2 kent de grote landtunnel. Omdat het omringende, tot tunneldak opgehoogde maaiveld van die landtunnel hoger ligt dan de weg, is de door Rijkswaterstaat ingeschakelde landschapsarchitect Roel Bakker (BGSV) met het idee gekomen om ook het zuidelijke tracé dat aansluit op die tunnel vorm te geven als een verlaagde ‘zwarte’ rivier tussen groene dijken, refererend aan het Hollandse landschap. De omgeving van de weg is dus opgetild tot het niveau van de viaducten over de lager gelegen A2 heen en met dijktaluds van 6,5 m hoogte fungerend als geluidschermen. Eigenlijk is het een tunnel zonder dak, maar met enkele dwarsverbindingen. Zo kun je prima het gebied overzien, ook vanuit de nieuwe woningbouw van Leidsche Rijn.” Een unieke inpassing dus van de weg, waarbij de nieuwe Stadsbaan, die op het niveau van het opgehoogde maaiveld parallel aan de westzijde van de A2 loopt, voor een belangrijke ontsluiting zorgt van Leidsche Rijn. Om die Stadsbaan te bereiken is het Marinus van Tyrusviaduct een belangrijke verbindingsroute, maar ook Hooggelegen en een fietsbrug horen tot die verbindingen.
Het hoogteverschil tussen de Stadsbaan en de A2 gaf tegelijkertijd aanleiding voor fraaie architectonische oplossingen. Zo heeft landschapsarchitect Roel Bakker bij de aansluiting van Hooggelegen de op- en afritten samen met geluidsschermen daarlangs - van buitenaf gezien als één muur - als een ‘krul in het water gezet’ waarbinnen de afrit omhoog klimt. “De opgave was om zo compact mogelijk die op- en afritten te realiseren, vandaar een geminimaliseerde krul. Met schanskorven is de krulvorm fraai geaccentueerd. Ook bij een onderdoorgang voor fietsers is met medewerking van landschapsarchitect Harm Veenenbos, uit oogpunt van sociale veiligheid, een kolomvrije overspanning gemaakt en is een vorm gekozen van vlakke, iets achterover hellende doorlopende wanden, zodat geen enge hoekjes ontstaan. Tevens heeft Herman Kuijer een lichtkunstobject voor deze tunnel ontworpen, waarbij de onderdoorgang extra aantrekkelijk wordt voor de gebruikers.”
Uitvoering voert regie
Bij het Marinus van Tyrusviaduct had de gemeente Utrecht een hoog ambitieniveau voor het ontwerp van het viaduct. Paul van der Ree van Studio SK ontwierp het viaduct als een soort boogoverspanning over de A2. Aangezien dit het eerste viaduct bij Utrecht is voor de automobilist vanuit het zuiden, symboliseert de boog de poort van Utrecht, compleet met een hoog lichtobject. Paul Scheublin: “De functionele praktijk heeft grote invloed gehad op dit ontwerp en heeft in feite de regie overgenomen. Het viaduct moest plaats gaan bieden aan een rijbaan voor auto’s, een fietspad en een baan voor hoogwaardig openbaar vervoer. Vanwege de voortschrijdende woningbouw in Leidsche Rijn wilden wij die HOV-baan vooruitlopend op het gereedkomen van de A2 snel gerealiseerd hebben. Dat betekende dat er ruimte gevonden moest worden voor de pijlers in het bouwproces van extra rijbanen en het daarbij steeds verschuiven van verkeer. Je moet tenslotte 120 m overspannen en daar heb je pijlers bij nodig.”
“Het door de reconstructie van de A2 telkens verschuiven van de rijbanen maakte het moeilijk een plaats te vinden voor de pijlers,” vervolgt de projectmanager. “In die fase heeft Rijkswaterstaat voorgesteld om een overspanning van 120 m (parallelbaan-rijbaan-rijbaan-parallelbaan) te realiseren. Maar een dergelijke overspanning, vergelijkbaar met een brug over het Amsterdam Rijnkanaal, zou een erg dure oplossing worden. Wat kost een m2 viaduct en wat kost een pijler? Uiteindelijk bleek het mogelijk een plaats te vinden voor een middenpijler en een pijler tussen de westelijke hoofd- en parallelbaan. Voor de oostzijde bleef een grote overspanning van circa 55 m onvermijdelijk.
Omdat 55 m toch een dure overspanning is, kwam de gedachte op om deze overspanning in de lengterichting in twee delen te knippen en zo alleen het HOV-deel naar voren in de tijd te trekken en het tweede deel later te bouwen als er wel een extra pijler kon worden geplaatst. Dat bleek een interessante besparing te geven. Vervolgens bedacht de stedenbouwkundige dat hij die twee delen dan ook uit elkaar kon trekken, wat mooier aansloot bij de wegenstructuur in Papendorp. Zo ontstond het idee voor de vorkconstructie, waarbij we eerst de ene poot met een grote overspanning en in fase twee de andere poot met extra pijler konden realiseren. Met een extra grote overspanning voor de eerste vorkpoot, een verbindingsstuk op een plaats waar dit goed te bouwen zou zijn en het verkeer weinig hinder ondervond en een korte overspanning in prefab bij de steel van de vork. Je verwacht vooraf niet dat je met een complexer en mooier viaduct in twee fasen gebouwd goedkoper uit bent, maar deze aanpak in techniek en vormgeving leidde inderdaad tot de beoogde kostenbesparing. Eigenlijk is de fraaie vorkoplossing dus door bezuinigingen ontstaan. Het bewijst dat een mooie mix van ontwerp en techniek tot prachtige resultaten kan leiden, zowel in esthetisch eindresultaat als in kosten van aanleg.” En voor de toekomstige A2-berijder die daar een constructief oog voor heeft, blijft het raadselachtig waarom er twee viaducten vlak na elkaar staan, waarbij de eerste het met een pijler minder kan doen.
Opengesteld
Met het ontwerpbeeld is de gemeente naar Rijkswaterstaat gegaan, die het heeft ingebracht in de Alliantie van opdrachtgever (RWS) en bouwcombinatie Traject Novum. Zij kregen de vrijheid om het ontwerp in te vullen. “De aanbesteding volgens het alliantiemodel stond niet toe dat onze architect voor de uitwerking van het ontwerp zou worden ingezet, maar de Alliantie heeft hem logischerwijs er wel bij gehaald voor die verdere uitwerking. De Alliantie heeft ontwerp en techniek bepaald. De eerste poot kon in 2009 in gebruik worden genomen, de tweede poot is eind 2010 voor alle verkeer opengesteld. Het wachten is op de openstelling van de landtunnel, die nog wordt aangepast en getoetst op veiligheidsmaatregelen. Als die open kan - verwachting is tweede helft 2012 - kan het volledig verbrede tracé van de A2 in gebruik worden genomen. De bruggen en viaducten zijn eind 2010, uitgezonderd viaduct 1 van de A2 over de Leidsche Rijn, allemaal opengesteld voor het verkeer.
Paul Scheublin is blij met het eindresultaat. “Wij hebben als gemeente Utrecht een duidelijke ontwerpfilosofie ingebracht. We hebben ook bewust niet deelgenomen aan de Alliantie, maar met Rijkswaterstaat een vast bedrag afgesproken voor de bouw van dit viaduct. Er is intensief door de bouwers en Spanbeton gezocht naar een goede manier om de beoogde toogvorm in het esthetische beeld te krijgen door met randelementen te gaan werken in combinatie met bijzonder lange, maar uniforme liggers voor de extra grote overspanning. Natuurlijk, de architect moet iets water bij de wijn doen, maar het architectonische beeld is recht overeind gebleven. Nogmaals, dit project draagt de kenmerken van een aantrekkelijk mix van architectuur en techniek.”
Projectgegevens
Opdrachtgever: Gemeente Utrecht
Ontwerp: Studio SK, Paul van der Ree
Design & construct: Rijkswaterstaat en Trajectum Novum;
Uitvoeringspartners: Aveco de Bondt, Visser & Smit Hanab, Holland Scherm, Volker Staal en Funderingen, Smits Neuchâtel en VWS Geotechniek
Prefab betonliggers: Spanbeton, Koudekerk a/d Rijn
Viaducten en bruggen in ‘Hooggelegen’ over de A2
door P. Engels
Ontwerp en uitvoering schuiven in elkaar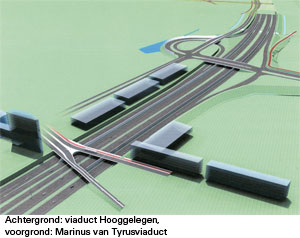
Technisch, organisatorisch en contractueel is de bouw van zeven bruggen en viaducten rond het knooppunt Hooggelegen boven de A2 van bijzondere allure.“Bij welk te bouwen viaduct of brug komt het voor dat ontwerp en uitvoering bijna parallel aan elkaar lopen? Twee maanden na de laatste tekening, is het werk buiten klaar” aldus senior- projectcoördinator Mark Veenma van de aannemersalliantie Trajectum Novum Van Hattum en Blankevoort. “In het ontwerp wordt veel aandacht besteed aan de technische maakbaarheid. Zo praat je in de ontwerpfase bijvoorbeeld al met de prefab-betonfabrikant over een oplossing voor extra lange kokerliggers. Deze projectfasen ontwerp en uitvoering schuiven in elkaar. Het zijn stuk voor stuk bruggen en viaducten waarbij steeds keuzes zijn gemaakt voor het beste ontwerpresultaat én de uitvoeringstechniek.”
Zeven bruggen en viaducten over en parallel aan de A2 tussen Oudenrijn en Hooggelegen worden uitgevoerd door een bijzondere samenwerking in alliantieachtig verband. Rijkswaterstaat en Trajectum Novum zijn gezamenlijk verantwoordelijk voor het ontwerp en de uitvoering van het project, met tevens een directe samenwerking met convenantpartner de Gemeente Utrecht. In deze verregaande vorm van samenwerking bundelen de partners hun kennis om complexe infrastructurele werken slim en efficiënt uit te voeren, met zo weinig mogelijk verkeershinder.
Op een relatief klein wegvak met een lengte van 1,7 km, ter grootte van een ‘postzegel’, worden de volgende kunstwerken gerealiseerd:
• een nieuw viaduct in de A2 over de Leidsche Rijn en de daarnaast gelegen fietsverbinding;
• het nieuwe viaduct Hooggelegen dat in de plaats komt van de beide overbekende voormalige betonnen boogbruggen;
• het Marinus van Tyrusviaduct, een vorkvormig nieuw viaduct tussen de wijken Papendorp en Leidsche Rijn;
• een nieuw viaduct in de Stadsbaan over de Leidsche Rijn en de daarnaast gelegen fietsverbinding;
• twee viaducten van de Stadsbaan over de toe- en afrit van de A2 in de Krul nabij de aansluiting Hooggelegen;
• een fietsbrug over de Leidsche Rijn met een kunststof dek voor een doorgaande fietsroute van Utrecht centrum naar de wijk Leidsche Rijn.
Elk viaduct heef zijn eigen bijzonderheden in vorm, technisch ontwerp, uitvoeringsmethode en hulpconstructies. Ook de fasering, verkeerskundige maatregelen en de vrije bouwruimte waren van invloed op het ontwerp en de te kiezen werkwijze. Per viaduct waren er bepaalde vrijheden in ontwerp en uitvoeringsmethodiek, maar allemaal met intensieve samenhang tussen deze twee projectfasen. De bouw van nagenoeg alle viaducten is inmiddels afgerond.
Raakvlakken opzoeken
Mark Veenma vervolgt: “In de praktijk betekent de alliantiesamenwerking dat alle partijen zich buigen over ontwerp, voorbereiding en uitvoering. Waar zitten de raakvlakken? Als je een keuze maakt in het ontwerp, hoe werkt die keuze door in voorbereiding en uitvoering? Deze werkwijze vraagt het nodige van de mensen. Het is een continue interactie! Je doet het samen met het hele team.”
De innovatieve werkwijze is voor de te bouwen bruggen en viaducten zonder noemenswaardige problemen verlopen. Veenma: “Natuurlijk kom je af en toe verrassingen tegen. Zo moesten wij tijdens de uitvoering van het viaduct over de Leidsche Rijn op het laatste moment de heipalen vervangen door boorpalen. Maar dat was in feite de grootste verandering tijdens de rit. Wel zijn juist in de ontwerpfase, waarbij je naar de maakbaarheid kijkt, zaken soms rigoureus omgegooid. Zo was bij één van de zeven viaducten, het Marinus van Tyrusviaduct (zie ook het volgende artikel), de gedachte om de randligger vanwege de toogvorm in één stuk in het werk te storten. Dit is omgezet in prefab elementen met cannelures om het beeld van één geheel én de toogvorm te verkrijgen, maar ook om de uitvoeringstechnische haalbaarheid. De randelementen en leuningen zorgen voor de toogvorm, terwijl de kokerliggers vrijwel vlak konden blijven. Met een ietsje bolling om visueel juist recht te ogen bij zo’n lengte. Het is een goed compromis geworden.”
Mark Veenma: Als een architect een bepaald beeld heeft neergezet en je komt met voorstellen om dat qua uitvoeringstechniek te veranderen, dan kom je wel aan z’n kindje. We hebben de architect er dan ook steeds bijgehouden en gezocht naar consensus. Als je kijkt naar technische maakbaarheid en risico’s dan is daar begrip voor, zolang de visualisatie in beeldeffect overeind blijft. Dat overleg over en weer tussen architect en bouwers is een goede zaak geweest. We hebben ervan geleerd voor volgende projecten.”
Supersnel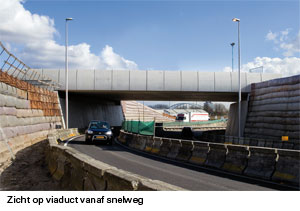
De senior-projectcoördinator blikt nog eens terug op het hele proces: “In november 2007 is de alliantie begonnen met het ontwerp. In de bouwvakvakantie van 2008 zijn wij met de bouw gestart. Krap twee jaar later waren de meeste kunstwerken gerealiseerd. Dat is echt supersnel. Je hebt misschien niet zelf het idee dat het bijzonder is geweest, maar velen spreken van een huzarenstukje. En als je nagaat dat men vooraf rekening hield met een vijftal weekendafsluitingen van de A2 voor bouwwerkzaamheden en het is er geen eentje geworden, dan hebben wij ruimschoots aan de eis ‘minimale verkeershinder’ voldaan.
Opdrachtgever Rijkswaterstaat had namelijk vooraf deze eis op tafel gelegd. Daarom zijn we al in de ontwerpfase met Spanbeton gaan praten. Dan ga je met een ‘open mind’ zo’n proces in en breng je expertises samen. Je weet dat bouwen in prefab een grote invloed heeft op het ontwerp- en uitvoeringsproces. Je zult zaken van tevoren moeten vaststellen omdat prefab beton nog geproduceerd moet worden. Terwijl het tijdbestek kort is. Aan de andere kant biedt het snelle monteren van prefab liggers voordelen. We bedachten met Spanbeton een oplossing voor lange prefab betonliggers, die met eenvoudige politiestops en dus met minimale verkeershinder konden worden geplaatst. Als bouwers moet je normaliter lang van tevoren een weekendafsluiting plus reserveweekend voor de montage van betonliggers opgeven. Dit heeft meteen veel impact op je planning en organisatie. Ineens liggen die zaken vast. Kan dit niet anders? Dankzij een slimme opstelling van de kranen buiten het verkeer kon bij zowel het viaduct Hooggelegen als bij het Marinus van Tyrusviaduct over de drukke A2 worden gekozen voor het monteren met korte politiestops in de nacht. Dan wordt ligger voor ligger ingereden, door twee mobiele kranen aan weerszijden van het wegvak opgepakt en 10 minuten later ligt de ligger op z’n plek en kan het verkeer worden vrijgegeven. Dit proces herhaalt zich enkele keren in de nacht, totdat een weggedeelte is overspannen. Op die manier wordt met maximale montagesnelheid en minimale verkeershinder gebouwd.”
Maatwerk in liggers en landhoofden
Voor de reconstructie van het knooppunt Hooggelegen zijn lange betonliggers van circa 45 m lengte geplaatst. Voor het Marinus van Tyrusviaduct waren dat zelfs extra lange liggers (54,4 m). Mark Veenma: “Zo’n plus van circa 10 m maakt écht een groot verschil. Die lengte leidt verder tot een forse liggerhoogte (1,80 m). Door de liggers een meter smaller te maken kon het totale gewicht worden beperkt. Zo ben je aan het zoeken naar de optimale ligger in een bepaalde situatie. Dit geldt bijvoorbeeld ook voor twee viaducten van de Stadsbaan, waar wij de optimalisatie hebben gevonden in één type afgeschuinde ZIP-ligger, waarbij de flexibiliteit is gevonden in de landhoofden. Eigenlijk is dat de ideale situatie: standaardisatie van prefab delen en variatie in de landhoofden die je ter plekke maakt. Bij drie andere viaducten zijn bijvoorbeeld combiwanden als landhoofd toegepast. De combiwanden bestaan uit buispalen van ruim 20 meter lengte met ertussenin damwanden. Het is steeds zoeken naar een goed ontwerp dat uitvoeringstechnisch prima te realiseren is en dat tegelijkertijd aan de eisen van opdrachtgever en architect voldoet. Bij alle zeven viaducten van dit project is daarop met succes ingezet.”
Extra puzzelen
Bij alle zeven viaducten was het puzzelen in ontwerp en uitvoering. Enkele uitvoeringstechnische vraagstuk-ken vergden bijzonder veel creativiteit. Zo moest op de V-vork van het Marinus van Tyrusviaduct een lichtkunstwerk komen. De 24 m hoge lichtmast vangt echter de nodige wind. Veenma: “Dit moest worden opgevangen in het prefab betonnen dek. We zijn met Spanbeton volop aan het puzzelen geweest om dit technisch op te lossen. Een ander voorbeeld: bij het viaduct in de A2 over de Leidsche Rijn loopt onderlangs een fietstunnel. Onder het dek van het viaduct is een lichtkunstwerk bedacht die uit ongeveer 510 LED-lampjes bestaat. Zo kunnen fietsers een fraaie passage beleven. Maar dit betekende wel dat wij aan de onderzijde van een betonnen viaduct in de weer moesten met de vele kabels en leidingen voor dit lichtobject. Creativiteit hoort er gewoon bij. Je moet echter waar mogelijk niet elke keer het wiel opnieuw willen uitvinden. In de aannemerij moet je wel ondernemen en de dingen (meteen) goed doen en daar dus vooraf over nadenken. Dat is in elk geval de filosofie van Van Hattum en Blankevoort.”
Projectgegevens Marinus van Tyrusviaduct
Opdrachtgever: Rijkswaterstaat, namens gemeente Utrecht;
Design & construct: Rijkswaterstaat en Trajectum Novum (Van Hattum en Blankevoort, Mourik Groot-Ammers, KWS Infra, Boskalis en Vialis);
Ontwerp Marinus Studio SK, Paul van der Ree
van Tyrusviaduct:
Ontwerp snelweg: Paul Wintermans
Uitvoeringspartners: Aveco de Bondt, Visser & Smit Hanab, Holland Scherm, Volker Staal en Funderingen, Smits Neuchâtel en VWS Geotechniek
Prefab betonliggers: Spanbeton, Koudekerk a/d Rijn
Amsterdamse brugrenovatie ingrijpender dan gedacht
door P. Engels
Geschiedenis Basculebrug de Hogesluis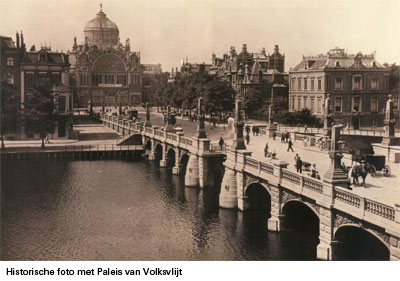
De Hogesluis (brug nummer 246) is een Amsterdamse monumentale dubbele basculebrug met tien doorvaarten, ontworpen in Parijse stijl, versierd met sierstukken van gietijzer (met stadswapen). Kenmerkend zijn verder de natuurstenen bekledingen op de koppen van de pijlers en de basculekelder, een vaasbalustrade, obelisken en ornamenten, alsmede gedecoreerde lantaarndragers met bijpassende lantaarns. De brug uit 1662 werd in 1883 door de huidige plaatbrug vervangen, ook met een beweegbaar gedeelte, uitgevoerd als dubbele basculebrug. Sinds 1904 rijdt tramlijn 10 over de brug en in 1905 is lijn 7 daar bijgekomen. In 1976-1977 is de brug ingrijpend gemoderniseerd. De bewegende delen hebben in de loop van de tijd, vooral bij warm weer, voor veel problemen gezorgd. Om dit temperatuurprobleem de baas te worden, is in 2003 een sproei-installatie aangebracht die het uitzetten van het stalen brugdek bij warm weer tegengaat. Gezien de staat van het brugdek - dat compleet op was - zou dit volgens het bestek worden vervangen door een nieuw brugdek met prefab betonnen liggers en een stalen basculebrug. Nader onderzoek naar de algehele staat gaf een ander resultaat dan was voorzien. Er moest een compleet nieuwe brug komen op nieuwe pijlers, kelders en landhoofden. In een bouwteam-setting hebben aannemer VBK, Gemeente Amsterdam als opdrachtgever (DIVV dienst infrastructuur verkeer en vervoer) en Spanbeton het ontwerp, de engineering en realisatie van het prefab brugdek ter hand genomen. Tijdens de renovatiewerkzaamheden kunnen het tramverkeer en het langzaam verkeer gebruikmaken van een noodbrug ten noorden van de brug Hogesluis. In de hulpbrug zijn beweegbare delen opgenomen, zodat de scheepvaart op de Amstel niet gehinderd wordt.
Een nieuwe brug met behoud van de authentieke uitstraling
Martin Eman van de VBK Groep uit Hoorn is projectleider op het werk, waar het drukke fiets- en tramverkeer passeert via de naastgelegen tijdelijke stalen noodbrug. Het werk is in de planfase compleet veranderd. Voor de brug is het goed uitgepakt, want deze is nu helemaal op de toekomst gericht met een lange levensduur. Daarbij zijn het beweegbare stalen dek en de bewegingswerken door BSB Staalbouw geheel gerenoveerd en die voldoen nu aan de huidige eisen. Het nieuwe brugontwerp is een technisch uitdagende opgave geworden. Neem bijvoorbeeld de innovatieve oplossing om het aantal dure glijopleggingen zoveel mogelijk te beperken. Of de slimme oplossing met een prefab betonnen bak half onder en boven de waterspiegel, zodat de constructie van met name metselwerk boven water ligt en niet door vocht kan worden aangetast. Wat organisatie betreft, er zijn niet minder dan 1700 authentieke natuurstenen (sier)elementen van de brug gehaald en die worden stuk voor stuk gerestaureerd en straks teruggeplaatst.
Het werk leek aanvankelijk gemakkelijker: er lagen een ontwerp en een RAW bestek. Op het moment dat duidelijk werd dat de Europese norm tot een zwaardere brug zou leiden, bleek na verdere destructieve onderzoeken dat de oude dragende brugconstructie niet meer volstond. De huidige renovatie bestaat uit het vernieuwen van de landhoofden, brugkelders, waterpijlers en het brugdek. De geïnventariseerde beschadigingen en gebreken aan de natuurstenen elementen worden hersteld. Ook voor deze onderdelen geldt dat behoud ervan, vanuit cultuurhistorisch oogpunt, de voorkeur heeft boven vervanging. Dit alles betekende voor DIVV en VBK de koppen bij elkaar steken. Martin Eman: “Wij kregen de ruimte om onze innovatieve kracht te benutten en specifieke oplossingen te bedenken. Dat was nodig bij dit complexe project. Voor het prefab brugdek is de expertise van Spanbeton van pas gekomen. Spanbeton hebben we laten meedenken over oplossingen. Want bij zo’n oude brug leg je niet - één twee drie - een paar standaard betonliggers neer. Je zit met afwijkende maatvoering, met veel kabels en leidingen voor de bediening, met stalen brugdelen die uitzetten en krimpen onder invloed van temperatuur. Kortom, er waren maatwerkoplossingen nodig. Uiteindelijk is gekozen voor verbrede liggers met versmalde flenzen. Op die manier werd een optimaal stramien voor het brugdek bedacht.” In totaal worden voor deze brug 144 stuks SJP350/990 liggers toegepast.
Over de eigen schaduw heen
Martin Eman: “Met drie in het vak kundige partijen, hebben wij ontwerp en engineering uitgedokterd. De opdrachtgever begreep dat wij daarvoor de ruimte moesten hebben. Als men vast blijft zitten aan de eigen insteek of eigen producten, kom je niet verder bij zo’n project. Je moet over de eigen schaduw heen springen en de moeite nemen naar elkaar te luisteren. Anders lukt het niet om te innoveren en te optimaliseren.”
Mooi voorbeeld zijn de glijopleggingen. “Je zit met betonnen ‘volstortliggers’ op een natuurstenen onderbouw. Dan rijst de vraag hoe je dat op elkaar gaat afstemmen. Komen er dure glijopleggingen of iets anders? We hebben ervoor gekozen om aan één kant de opleggingen momentvast in te storten en aan de andere kant en bij de kelders voor glijoplossingen te kiezen. Een andere doordachte oplossing betreft de prefab betonelementen die over de buispalen zijn aangebracht tot een halve meter onder water. In feite maak je een soort H, waarbij boven de waterlijn de elementen en de palen worden verbonden en het metselwerk wordt aangebracht. Deze constructies blijven dus boven water en hebben minder last van aantasting. De stalen hulpbrug die BSB Staalbouw heeft geplaatst, is eveneens een slim ontwerp. Er is één grote beweegbare klap en een vast deel. Tijdens de faseringen zijn deze snel te demonteren en om te draaien, zodat de scheepvaartroute snel kan worden aangepast. Want de scheepvaart moet natuurlijk doorgang vinden.”
Bij de Brug Hogesluis komt het zowel op ontwerp, engineering als uitvoering aan. “Het is echt een uniek project, waarvoor wij als team een mooi en uniek bouwwerk realiseren. Als de brug in 2012 gereed is, zal het oorspronkelijke uiterlijk van de ‘oude Brug’ te zien zijn. Maar met een binnenkern, gebouwd volgens de huidige normen, is de brug gereed voor de toekomst.”
Projectgegevens
Opdrachtgever: Gemeente Amsterdam (Dienst Infrastructuur Verkeer en Vervoer).
Architect: W.H. Springer.
Design & Construct: VBK Groep.
Prefab beton: Spanbeton.
Staalbouw: BSB Staalbouw.
Info: www.iba.amsterdam.nl
Kippenvel van indrukwekkend transport brugliggers
door P. Engels
Ontwerpuitgangspunten Productie en Transport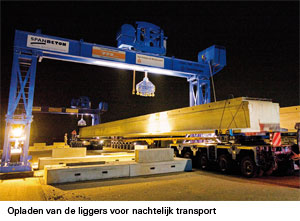
Onlosmakelijk liggen de productie van prefab betonnen brugliggers en het transport ervan naar de bouwlocatie, in elkaars verlengde. Bij beide worden met regelmaat grenzen verlegd. Aan de ene kant de engineering en productie van langere en soms zwaardere liggers. En aan de andere kant het transport met totaalgewichten tot 230 ton. De grenzen van het transport lijken te naderen, omdat er over de weg tot 250 ton mag worden vervoerd en daarnaast het maken van bochten niet oneindig is, binnen de alsmaar toenemende bebouwing.
Fred van der Meijden is algemeen directeur van Van der Meijden Transport en Beton Montage uit Koudekerk aan den Rijn. Hij is niet voor één gat te vangen, al zegt ook hij “ergens ligt natuurlijk wel de maat. Maar, als er grenzen om welke reden dan ook overschreden moeten worden, dan verzinnen wij gewoon wat nieuws, zoals vrachtwagens op pontons. Daarvoor hebben we gekozen toen er enorm grote liggers nodig waren voor het verbreden van de Hollandse Brug. Die transporten waren te zwaar om ze over de weg te laten rijden. Vandaar dat ze vanuit Koudekerk naar de Hollandse brug toe zijn gevaren. De vrachtwagens zijn vanaf de pontons aan land gereden en vervolgens via intern transport naar de bouwlocatie gereden”.
De samenwerking met Spanbeton dateert al vanaf de start van de betonfabriek. Van der Meijden: “het mooie is dat wij in onze samenwerking elkaar stimuleren om oplossingen te zoeken voor de combinatie productie en transport. Het ingenieursbureau van Spanbeton kan bijvoorbeeld slanker en dus lichtere liggers ontwerpen. Dan kunnen die liggers eventueel langer of hoger worden gemaakt, als men maar rekening houdt met het maximale tonnage. Op onze beurt denken wij als transporteur mee hoe een hoge ligger op een vrachtwagen met hydraulische vijzels stabiel wordt gehouden, bijvoorbeeld als de wagen van een ponton afrijdt waarbij instabiliteit kan optreden doordat de vrachtwagen heen en weer schudt.”Vrijwel elk transport is zowel uitdagend als leuk. Fred van der Meijden vervolgt: “Ik betrap mezelf erop dat we zowel met kleine als met grote elementen te maken hebben en dat elk een eigen inbreng heeft. Grote brugliggers met een massa van 112 ton en een lengte van 43 m kunnen nog vanuit Koudekerk over de weg getransporteerd worden door Alphen aan den Rijn heen. Met die 43 m lange elementen kunnen wij nog alle bochten in die gemeente nemen. Wordt de lengte groter en het gewicht zwaarder, dan steken wij met een tijdelijke brugconstructie de Oude Rijn over. Dankzij deze ‘vinding’ kunnen we inmiddels brugliggers vervoeren tot ruim 64 m lengte en 160 ton gewicht. Uiteraard gebeurt het overzetten ’s nachts, om het scheepvaartverkeer niet te hinderen. Bovendien moeten zware transporten steeds meer ‘s nachts plaatsvinden omdat het wegverkeer zo min mogelijk mag worden belemmerd.”
Maanden voorbereiding
Dergelijke projecten betekenen wel een hele organisatie voor het transport. Maanden van tevoren moet worden begonnen met het regelen van vergunningen. Dan volgt er een hele rits aan aandachtspunten qua planning en organisatie, van overleg over rijtijden, rekening houden met werk aan de weg en omleidingen, politiebegeleiding, rijsnelheid, tijdstippen van montage enz. Voorts wordt het personeel voortdurend geschoold in eisen rond verkeer, transport, veiligheid en rijvaardigheid. Daarnaast praat je over de inzet van bijzonder materieel. Het gaat wel om 100 wielen per vrachtwagen en over een enorme hoeveelheid hydraulische hulpmiddelen. Als een technisch schakeltje in die keten je in de steek laat, gaat drie maanden planning overboord. Toch doen wij er alles aan om juist op betrouwbaarheid uitstekend te scoren. Wij weten dat het bij die ene nachtelijke montage soepel moet verlopen, want de halve bouwketen is er dan mee aan de slag.”
In de voorbereiding is het een groot voordeel dat Spanbeton en Van der Meijden al zo lang een vaste relatie onderhouden, namelijk vanaf de dag dat Spanbeton werd opgericht in 1948. Bovendien zijn de beide bedrijven sinds 1977 buren, zodat men gemakkelijk voor overleg bij elkaar binnenloopt. Vraagstukken over transport en montage kunnen snel worden opgelost. Van der Meijden: “Het is een hecht samenspel geworden. Hierin zie je de meerwaarde van partners die wederzijds respect hebben en op elkaar kunnen vertrouwen. Die samenwerking betaalt zich op essentiële punten uit, want elk transport heeft zijn eigen vraagstukken. We hebben er al heel wat gereden, maar vaak staat het kippenvel me op de armen als ik een transport zie gaan en weet hoe we dit in voorbereiding en uiteindelijk transport hebben weten te klaren.”
Tijdelijke Maximabrug
Voor het werk Westrandweg met z’n vele grote brugliggers is een bijzondere oversteek over water van de Oude Rijn gemaakt. Van der Meijden: “Er is een tijdelijke pontonbrug gemaakt, de Tijdelijke Maximabrug geheten. Die ligt overdag langs de wal en wordt ‘s avonds laat via kabels en studpalen omgevaren tot die dwars over de Oude Rijn ligt. Over deze ontwikkeling zijn we al in 2005 gaan nadenken, samen met Hebo Maritiem. Toen waren het pontons die met een sleepboot op hun plaats werden gevaren, nu is het een ‘vaste’ invaarconstructie. Het werkt perfect. Via roll on roll off kleppen kunnen de vrachtwagens met brugliggers van 64 m en 160 ton over die tijdelijke brug rijden. Vervolgens gaan ze op weg naar Amsterdam, waar de liggers doorgaans tijdelijk worden opgeslagen, totdat ze voor montage in het werk worden afgeroepen. Over de Westrandweg gesproken, je hebt het wel over 3 kilometer viaduct, dat onder andere het spoor kruist. ”Het bezorgt mij extra kippenvel als ik bedenk dat er gedurende 2,5 jaar lang honderden brugliggers voor de Westrandweg in Amsterdam worden vervoerd. Zelfs met het gebruik van de tijdelijke brug wordt nog altijd voortdurend vooruitgang geboekt. Overigens hopen we in 2014 of 2015 een definitieve brugverbinding te hebben als vervanger van de tijdelijke Maximabrug.
Fred van der Meijden besluit: “Als je het spelletje een aantal keren hebt gespeeld, ga je steeds slimmer en efficiënter te werk. Dat geldt in algemene zin voor het ontwikkelen, produceren en transporteren van betonnen brugliggers. Dan rijd je bijvoorbeeld in één nacht zeven liggers naar de A2 bij Utrecht, even met voor- en achterwagen insteken, met twee kranen de ligger oppakken en in minder dan 15 minuten op zijn plaats monteren. Na een korte politiestop, die je ook moet regelen, rijdt het verkeer vervolgens ongehinderd door. Over een korte stop gesproken!
Familiebedrijf
In mei 1935 kocht Willem van der Meijden voor fl. 870 een gebruikte Fordson vrachtwagen. Daarmee werden bouwmaterialen vervoerd voor Duinker & Verruijt, de toenmalige betonfabriek. Het transportbedrijf groeide en er kwamen meer vrachtwagens. In de oorlogsjaren werd het grootste deel in beslag genomen, behalve twee die onder stro bij boeren waren verstopt. Na de oorlog kon zoon Willem jr. het bedrijf uitbouwen. met een geconfisqueerde Duitse Mercedes en Canadese legertrucks. Bij de wederopbouw moest veel voor de bouwsector worden gereden. Fred en Teun van der Meijden kwamen in de zaak en sinds enkele jaren hebben hun zonen posities in het management. Inmiddels heeft het bedrijf een discipline Aannemersbedrijf voor de montage van prefab elementen, Transportbedrijven, een Garagebedrijf, een Exploitatiemaatschappij voor bedrijfshallen en buitenterreinen en een participatie in Mulder Montage B.V., Alphen aan den Rijn. In totaal telt het bedrijf zo’n 100 medewerkers.
Landviaduct Westrandweg Amsterdam
door P. Engels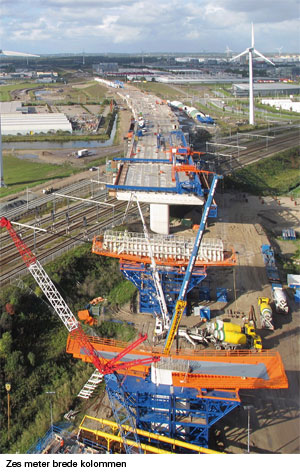
De Westrandweg zal de tweede Coentunnel en het knooppunt Raasdorp (A5/A9) verbinden. In opdracht van de Rijkswaterstaat wordt deze weg als een verhoogde snelweg (2 x 2 rijstroken plus vluchtstrook) aangelegd. Deze Westrandweg zal voor een betere toegang van de Amsterdamse havens in het Westpoortgebied zorgen. Het grootste deel van het ongeveer 10 km lange traject wordt aangelegd op een aarden baan. Meest spectaculair is kunstwerk 20, een ruim 3 km lang doorgaand viaduct dat op circa 12 m hoogte langs de Basisweg komt te liggen.
Ontwerp
Het ontwerp bestaat uit 27,5 m brede dekken, opgebouwd uit 10 prefab liggers. Deze liggers steunen op ter plaatse gestorte pijlerbalken. De pijlerbalken dragen hun belasting af aan een centrale kolom. Deze 6 m brede kolommen staan 44 m hart-op-hart.
Voor de Westrandweg heeft Spanbeton een nieuw type voorgespannen ligger ontwikkeld, de PIQ kokerligger. Het is een kokerligger met aan de onderkant aan beide zijden brede flenzen. Tussen de kokerliggers worden 2,8 m brede tussenliggers geplaatst alsmede twee randliggers. Een ter plaatse gestorte deklaag zorgt voor een vlakke bovenkant. De standaardliggers zijn 42 m lang en wegen 145 ton. De liggerhoogte bedraagt slechts 1,45 m wat slanke dekken oplevert.
Ing. Robert de Haas, projectdirecteur namens de Combinatie Westpoort wist van tevoren dat de combinatie met een apart iets moest komen, wilde ze kans maken dit niet-alledaagse landviaduct met vele kruisingen boven wegen, spoorwegen en een vaart te verwerven. De crux bij het 10 km lange tracé tussen de A5 en de tweede Coentunnel zit in het 3,3 km lange landviaduct, het grootste van Nederland. De Haas: “Hier moesten we het verschil kunnen maken”.
Stap één in de tender is het werk écht willen aannemen en dus bereid zijn op een redelijk diepgaande manier er tijd en energie in te steken. De Haas: “Je moet zo’n project op een verantwoorde manier kunnen maken, binnen een beheerst risicoprofiel. Maar je moet wel je nek uitsteken. Dat kon bij dit project, omdat je praat over bijna 100.000 m2 brugdek. Dit maakt het aantrekkelijk om daarvoor een uniek ontwerp te maken. Er is de samenwerking opgezocht met Spanbeton. Je weet dat je niet met standaard liggers aan moet komen, omdat je daarmee niet het onderscheid met de concurrent maakt. Het boek met standaardliggers moest opzij worden gelegd. Met open mind hebben wij vanaf nul zitten brainstormen over een slim ontwerp. Cruciaal was een optimale integratie tussen ontwerp en bouwmethode, alsmede een zo laag mogelijk eigen gewicht. Dan kun je immers de onderbouw en funderingen minder zwaar maken en kunnen grote overspanningen gerealiseerd worden met minder steunpunten. Er is een nieuw type kokerligger ontwikkeld, met twee vleugels, de PiQ-ligger. Het is een extra brede ligger van 2,80 m. Omdat het dek 28 m breed is, kun je met 10 liggers van 40 tot 45 m lengte volstaan voor een vloerveld. Twee liggers per dag produceren is haalbaar, dus kun je elke week op dinsdag een heel vloerveld monteren. Uiteindelijk wordt in het werk met behulp van bekisting ook boven de vleugels beton gestort, om het wegdek te completeren. Met die tien liggers per week maak je een efficiënte slag in je bouwproces.
Datzelfde geldt voor de extra lange betonliggers van 62 m - nog niet eerder toegepast in Nederland - die vanaf februari 2011 worden gemonteerd over de Haarlemmertrekvaart en de Ringvaart om de Haarlemmermeer. Je zoekt technisch de grenzen op en dat is ook nodig bij zulke projecten.”
Cultuurverschil
Hoewel Van Hattum en Blankevoort in meer projecten samenwerkt met Spanbeton en er onderling vertrouwen is opgebouwd, is er in de basis wel een cultuurverschil, meent Robert de Haas. “Een fabrikant van prefab beton zal bij voorkeur uitgaan van een bepaalde uniformiteit en dus opteren voor standaardmatige liggers. Als bouwer wil je elke keer projectspecifieke oplossingen aandragen, soms zelfs met de neiging het wiel opnieuw uit te vinden. Bij de Westrandweg was het essentieel om elkaar als strategische partners te versterken. We moesten het midden vinden tussen enerzijds een projectspecifieke aanpak met een ‘op maat’ oplossing en anderzijds het toch zo ‘standaard’ houden dat het in de totale aanpak profijt oplevert. Met 850 PiQ-liggers praat je over een efficiënte, seriematige aanpak en tegelijkertijd over een projectgerichte oplossing met goed doordachte brugdekvelden en een lichte onderconstructie. De Westrandweg ligt op 85 éénkoloms steunpunten, waardoor de ruimte onder de weg maximaal kan worden benut. Dat bleek een groot winstpunt in het ontwerp.”
Over het innovatieve ontwerp en de engineering zijn vanzelfsprekend de nodige technische vragen gesteld, zeker door opdrachtgever Rijkswaterstaat. Het gaat immers om een nieuw type ligger, waarbij de onderbouw een bijzondere vormgeving heeft gekregen. Uiteraard zijn de berekeningen getoetst en zijn de keuringsprotocollen voor zaken als doorbuiging en scheurvorming doorlopen. De vragen werden nog nadrukkelijker toen het idee werd gelanceerd om de montage van de liggers met een speciale lanceerinrichting (Launching Gantry) uit te voeren. Robert de Haas legt uit: “Gebruikelijk is dat we in Nederland brugliggers monteren met kranen. Bij dit project heb je te maken met heel veel verkeer rond Amsterdam en met het moeten monteren boven wegen, dubbele spoorbanen en een drukke vaart. Het is een moeilijk bereikbare locatie met veel omgevingshinder vanuit de bouw. We hadden in Italië zo’n lanceerinrichting voor liggers aan het werk gezien, maar niet op de huidige grote schaal van de extra brede en zware betonliggers (150 ton gewicht per stuk). Het zou echter een mooie oplossing zijn voor dit project. Vanwege de onbekendheid is er vaak vanuit risico-overwegingen veel voorzichtigheid, maar als je ergens in gelooft, moet je doorzetten”.
Hercules
Eind april 2010 werd met de montage begonnen. Bij de tweede ligger ging het echter mis. De hele montage-installatie van 110 m lengte ging bij het hijsen van de ligger aan de achterzijde onderuit en het werk kwam een tijd stil te liggen. Pas in september 2010 kon de montage voortvarend worden opgepakt. Inmiddels worden de liggers in hoog tempo gemonteerd. De lanceerinrichting, ook wel Hercules genoemd vanwege de combinatie van slimheid en kracht, doet zijn werk prima. Het is een prachtige blikvanger deze gigantische installatie boven het maaiveld. Vanuit heel veel landen, tot China aan toe, zijn delegaties het werk komen bezoeken.
“Wij ervaren dagelijks dat de meerwaarde van de deskundigheid van partijen het proces ten goede komt. Als je ziet hoe we binnen een bouwproces kunnen samenwerken en optimaliseren, dan zou je van het prijsvechten af moeten. Gelukkig zie je dat grote opdrachtgevers in de infrastructuur andere factoren dan de prijs steeds meer laten meewegen. Minimale verkeershinder, bouwsnelheid, beheersbare risico’s, integrale veiligheid, het telt allemaal mee. Dan heb je als bouwer nóg meer kans om met slim ontwerpen, doordachte engineering en efficiënte bouwwijzen iets toe te voegen. We weten dat het bouwen zélf voor een opdrachtgever als Rijkswaterstaat meer en meer bijzaak wordt. Bouwers zullen van meer markten thuis moeten zijn dan alleen het bouwen zelf en bijvoorbeeld zaken als omgevingsmanagement, het regelen van vergunningen, een goede werkwijze voor kabels en leidingen, een logische planning en gedegen bouwcommunicatie moeten kunnen verzorgen. Dat vergt projectmanagers die ook op die terreinen thuis zijn. Maar wel het liefst mensen met een technische achtergrond, want techniek blijft een belangrijke rol spelen”.
Lange voorbereiding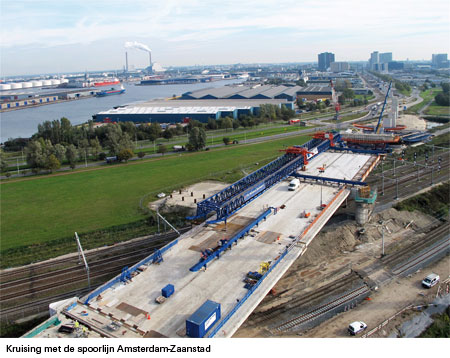
De uitvoering van de Westrandweg kende een zeer lange voorbereidingstijd. Nadat medio 2006 de opdracht aan de combinatie Westpoort werd verstrekt, liepen er nog tracéprocedures. Daarom werd erbij gezegd dat ontwerp en engineering konden worden uitgewerkt, maar dat de bouw nog niet zeker was. Die onzekerheid duurde nog een jaar langer dan gedacht. Pas op 29 juli 2009 gaf de minister uiteindelijk groen licht voor de realisatie van de Westrandweg. Robert de Haas: “Het voordeel was dat wij in de voorbereidingstijd ontwerp en plan klaar hadden gemaakt. Zodoende konden wij snel beginnen met de bouw en zal het werk in 2012 klaar zijn. Bij Design & Build contracten is de tijdsdruk tussen ontwerp en uitvoering vaak een probleem. Dat is jammer, want dan is er onvoldoende tijd om diepgaand naar innovatieve ideeën te kijken. Als dan later iemand zijn of haar vinger opsteekt met een slimme gedachte, kan dat door de tijdsdruk niet gehonoreerd worden. Je ziet echter bij een project als de Westrandweg dat optimalisaties een geweldig effect kunnen hebben”.
Ontwikkelingen in de bruggenbouw
Robert de Haas is van mening dat de nodige ontwikkelingen in de bouw van bruggen en viaducten te verwachten zijn. Hij denkt aan:
• grotere overspanningen;
• nieuwe oplossingen in transportmogelijkheden;
• nieuwe materialen als hogesterktebeton en dus slanker en lichter construeren;
• toenemende aandacht en klantwaardering voor vormgeving en beperking bouw- en verkeershinder;
• meer boven elkaar bouwen ter beperking van ruimtebeslag.
Vooruitdenken
De Westrandweg en Tweede Coentunnel zorgen ervoor dat Noord-Holland noord beter bereikbaar wordt. De A10 langs Amsterdam wordt ontlast omdat naar verwachting zo’n 30% van het verkeer in noord/zuidrichting gebruik gaat maken van de nieuwe snelweg. Tegelijkertijd zorgt de Westrandweg voor een betere bereikbaarheid en ontsluiting van het drukke Amsterdamse havengebied Westpoort. Dit gebied heeft nu enige overlast door de bouw met omleidingen en afsluitingen, maar de bouwmethode met de lanceerinrichting beperkt de overlast aanzienlijk. Ook voor andere overspanningen worden slimme, hinderarme methoden bedacht. Zo is in pakweg twee uur een dwarsligger over het spoortracé Amsterdam-Sloterdijk - Zaandam geplaatst. Een kolompijler met daarop de dwarsligger draaide in zijn geheel 60 graden over het spoortracé. De pijler en dwarsligger zijn eerst aan de rand van het spoorwegtracé vervaardigd. De dwarsligger is 27 meter lang en heeft een gewicht van 1 miljoen kilo. Het indraaien van de pijler met dwarsligger op deze schaal was nog niet eerder uitgevoerd. Door gebruik te maken van deze techniek is voorkomen dat tijdens de realisatie van de passage over het spoortracé het treinverkeer tussen Amsterdam-Sloterdijk en Zaandam voor langere tijd gestremd moest worden.
Robert de Haas: “Om gedurende een weekend een buitendienststelling te verkrijgen, moesten we dit anderhalf jaar van tevoren organiseren. Het bewijst dat het bij dit soort projecten niet alleen op techniek aankomt, maar ook op organisatie.”
Projectgegevens
opdrachtgever: Rijkswaterstaat
design en construct: Combinatie Westpoort (Van Hattum en Blankevoort, Boskalis en KWS)
bouwtijd: 2009 - 2012
Spanbeton historisch overzicht
door ir. C. Quartel, Manager Infra Spanbeton, Koudekerk a/d Rijn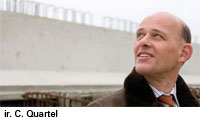
Spanbeton is in 1948 opgericht door betonfabriek Duinker en Verruijt NV te Alphen aan den Rijn en Van Hattum en Blankevoort NV uit Beverwijk. De onderneming begon zijn bestaan als N.V. Nederlandse Spanbeton Maatschappij (NSM). Doel van de onderneming was het fabrieksmatig vervaardigen van elementen van voorgespannen beton. Uit een voorafgaande verkenning was duidelijk geworden dat dit nieuwe concept toekomst zou hebben in de wederopbouw van Nederland.
De basis van deze vervaardiging is, tot op de huidige dag, het principe van voorspannen met voorgerekt voorspanstaal. Hierbij worden voorspandraden of strengen door een bekisting geleid die zich op een spanbank bevindt. Nadat de strengen op spanning zijn gebracht kan het beton in de bekisting (mal) worden gestort. Als het beton voldoende is verhard, neemt men de primaire spankracht op de uiteinden van de voorspandraden of strengen weg. Nu zouden de voorspanstrengen weer willen verkorten, maar het inmiddels verharde beton belet dit dankzij de perfecte aanhechting tussen het beton en het voorspanstaal. De strengen blijven dus uitgerekt maar geven daardoor de itrekkracht als reactiekracht over op het betonproduct. Zodoende wordt dat element door een drukkracht (voor)belast.Dankzij de Nederlandse Spoorwegen, die interesse toonde in de vervaardiging van voorgespannen portalen voor de elektrificatie van het spoorwegnet, kon een eerste start worden gemaakt op het terrein van Duinker en Verruijt NV aan de Gnephoek in Alphen aan de Rijn. De eerste productie van de nieuwe onderneming betrof de vervaardiging van voorgespannen dakspanten voor de eigen te bouwen fabriek. Na een moeilijke aanlooptijd werden in totaal 4500 elektrificatieportalen geproduceerd, goed voor 340 km spoorlijn. De voorspanning werd toen nog aangebracht in de vorm van dunne draden die door de stijlen voerden en in de top van het portaal via een afbuigpunt bijna over 180 graden werden teruggebracht naar de voet.
De eerste bruggen
Het productieprogramma werd al snel uitgebreid met dwarsliggers, ook in opdracht van de Nederlandse Spoorwegen, overigens werden de dwarsliggers toen nog niet voorgespannen.
Bij de viering van het 5-jarig jubileum waren ook betonnen voorgespannen balken onderdeel van het leveringspakket geworden. Zelfs in lengten tot 20 meter. Verder werden de zogenaamde Muwi balkjes geproduceerd voor het vloersysteem van NV Muijs en De Winter. Al snel werd Spanbeton betrokken bij de bouw van bruggen en viaducten. In het fotoalbum van Spanbeton treffen we een foto aan van de eerste brug in het jaar 1951, drie jaar na de oprichting. In 1953 werden liggers geleverd voor een serieus project, viaduct Rozenlaan te Rotterdam. Dit viaduct werd eerder gebouwd dan de A20 die er nu onderdoor gaat. Het vervult nog steeds een belangrijke functie in de infrastructuur van Rotterdam-Noord.
Aanvankelijk bestond er geen documentatie op het gebied van normen en voorschriften met betrekking tot het ontwerp en de berekening van fabrieksmatig voorgespannen beton, gebaseerd op de directe aanhechting tussen de voorgerekte draden en het daarna aangebrachte beton. Daarom begon men met het uitvoeren van experimenten en proeven in een zelf gebouwd bedrijfslaboratorium. Deze activiteiten werden Elektrificatieportalen uitgevoerd onder leiding van ir. A.S.G. Bruggeling, de ir. C. Quartel Viaduct Rozenlaan Rotterdam latere hoogleraar Betonconstructies van de TU Delft. In het bijzonder werden proeven gedaan op dwarskracht en proeven om te kunnen bepalen hoe de overdracht van de krachten in de voorspandraden- en strengen op het beton plaatsvond. Verschillende van de huidige rekenregels uit de VBC zijn nog gebaseerd op de kennis die toen door deze onderzoeken werd verkregen.
Liggersystemen
In die tijd werd een begin gemaakt met het standaardiseren van liggersystemen voor de bruggenbouw. Bekend werden de INP, RNP, TNP en SNP balken. Voor een grotere toepassing werden de liggersystemen samengebracht in publicaties onder de naam NSM productieprogramma. Daarin waren ook de bekende draagvermogengrafieken opgenomen. Verder kan nog vermeld worden dat NSM zich als toepasser van het naspansysteem met de zogenaamde Dywidag-staven ontwikkelde. Dit kwam voort uit de wens om oplossingen te creëren waarbij de verbindingen tussen prefab onderdelen dankzij de voorspanning, duurzaam en hoogwaardig zouden kunnen functioneren. Zo werden
balk-kolomverbindingen voor utiliteitsbouwprojecten door middel van deze techniek uitgevoerd. Tevens werden prefab liggers voor brugdekken statisch onbepaald gemaakt door het aanbrengen van naspanning met staven.
NSM ontwikkelde daarvoor de zogenaamde NSMverankeringen en verrichte zelf naspanwerkzaamheden.Al in de jaren ’50 bracht NSM een bijzonder concept op de markt, het zogeheten preflexbalkensysteem. Dit systeem combineert de gunstige eigenschappen van beton en staal in optimale vorm: een voorbelaste stalen balk wordt oorzien van een betonomstorting van de onderflens. Deze betonomstorting komt na het wegnemen van de voorbelasting onder een drukspanning. De zo ontstane samengestelde doorsnede is hierdoor in staat grote uitwendige belastingen op te nemen. Het is een mooi staaltje voorgespannen betontechniek. In 1971 werden al preflexbalken met een lengte van 37,5 meter toegepast. Dit werd gedaan om een grotere afwijkende overspanning van een kunstwerk in de A1 bij Naarden, over de Naarder trekvaart, met een totale constructiehoogte van slechts 1260 mm mogelijk te maken. Hoewel de preflexbalk in allerlei constructies werd toegepast, was het toch vooral de preflex pijlerbalk die de specifieke eigenschappen bewees, namelijk een slanke ondersteuningsconstructie met een zeer geringe zooldikte onder het prefab liggerdek uitkomend. De jaren 70 kenmerkten zich als de tijd van verandering. Spanbeton BV (de naam NSM was verlaten) bracht met regelmaat Technische Bulletins uit waarin naast vernieuwingen in het leveringspakket, technische beschouwingen werden gepubliceerd. Het bulletin van september 1970 opent met de volgende zin:
“Door de ervaring van Spanbeton bij de bouw van meer dan 900 bruggen in de achter ons liggende 20 jaren, zijn wij ervan overtuigd dat voor een optimale industriële productie standaardisatie een eerste vereiste is”.
Het betreffende bulletin introduceerde het nieuwe HIP liggersysteem, een systeem van liggers met een werkende breedte van 1200 mm in de vorm van een omgekeerde T die samen met een in situ gewapende druklaag van 160 mm een balkroosterdek vormde. De bijbehorende TRA randligger (in de vorm van een T) completeerde het bouwsysteem. Men dacht met deze nieuwe standaard een antwoord te kunnen geven op de vraag naar grotere overspanningen in economische oplossingen.
Standaardisatie
Achteraf is het interessant om vast te stellen dat hier een eerste periode van 20 jaar pionieren en uitproberen in voorgespannen beton werd afgesloten. Er volgde een nieuwe periode, ook van ongeveer 20 jaar, waarin de gestandaardiseerde systemen en methoden werden ontwikkeld. Deze vormen tot op de dag van vandaag de basis van de prefabsystemen van bruggen en viaducten in de Nederlandse markt.
Zo werd in 1973 het ZIP liggersysteem geïntroduceerd, een identiek systeem als het HIP liggersysteem maar met een aantal verzwaringen (vandaar de Z van zwaar) om aanrijdingsbestendigheid van het brugdek te verzekeren. ZIP liggers werden en worden nog steeds aangeboden in constructiehoogten variërend van 500 tot 1700 mm, in stappen van 100 mm. Het overspanningsbereik is 15 tot 45 meter.
In 1975 werd het SDK systeem toegevoegd; de letters staan voor Spanbeton Dywidag Kontakt systeem. Daarmee werd aan de markt een systeem gepresenteerd waarmee kwalitatief hoogwaardige relatief dunne brugdekken in een zeer korte bouwtijd konden worden samengesteld met een slanke, dat wil zeggen relatief kleine constructiehoogte. Dit allemaal dankzij een door Dyckerhoff und Widmann uit Duitsland in 1961 bedacht systeem waarbij een viaduct wordt gebouwd door rechthoekige liggers koud tegen elkaar aan te plaatsen en vervolgens in dwarsrichting na te spannen. Zodoende zou het viaduct zelfs demontabel kunnen zijn. Spanbeton verbeterde en industrialiseerde dit beginsel tot SDK. Anders dan bij de ZIP liggers warener maar twee beschikbare typen: SDK 650 en SDK 900, waarmee tevens de hoogte van het profiel wordt aangeduid. Met een SDK 900 profiel zou een overspanning tot 30 meter gerealiseerd kunnen worden. Bij de introductie waren de verwachtingen hooggespannen. Men ging er vanuit dat het merendeel van de viaducten in de toekomst zou worden gebouwd met dit systeem en daar vanuit gaande werd ook geïnvesteerd in een nieuwe productiehal. Dit was mede nodig omdat elk brugdek voorafgaand aan de werkelijke montage op de bouwplaats ook eerst in de fabriekshal werd opgebouwd om de zogenaamde contactvoegen tegen de
basisvorm van de liggers aan te storten. Opgemerkt mag worden dat er aanvankelijk veel belangstelling voor dit systeem bestond. Het leidde tot een aanzienlijke hoeveelheid opdrachten. Ongeveer 10 jaar later werden de voordelen van het systeem verder doorontwikkeld in het SKK kokerbalkensysteem. SDK liggers werden alleen nog toegepast in die situaties waarbij de factor tijd doorslaggevend was zoals bij spoorviaducten. Het SKK systeem werd dus in de jaren ’80 ingevoerd. Het voorzag in rechthoekige profielen met een breedte van 1180 mm. De hoogte varieerde van 700 tot 1400 mm. Een statisch bepaald brugdek werd verkregen door de liggers met een kleine voegafstand van minimaal 20 en maximaal 200 mm naast elkaar te plaatsen via gewapende rubberopleggingen op de ondersteuningsconstructie. De zijvlakken van de liggers waren aan de bovenzijde van een sponning voorzien van 30 mm diepte en 300 mm hoogte. De ruimte tussen de liggers werd dan over deze sponninghoogte met betonspecie gevuld en na verharding hiervan kon de dwarsvoorspanning worden aangebracht en gespannen. Het brugdek was hierna constructief gezien klaar en kon bijvoorbeeld door een mobiele kraan worden belast om de balken van de naastliggende overspanning te plaatsen. Om gewicht te besparen waren de liggers inwendig gevuld met piepschuim blokken waardoor de betonvorm de gedaante kreeg van een “holle” kokerbalk. In die begintijd waren de zijwanden slechts 120 mm dik en de boven- en onderflens respectievelijk 160 en 140 mm!
Deze kokerliggers boden aantrekkelijke voordelen: dankzij de vorm en hoge sterkteklasse van het beton, B65, waarbij het rijdek als het ware al was geïntegreerd in de balk, kon een overspanning worden gemaakt voor de zwaarste verkeersklasse 60 volgens de VOSB met een slankheid van 30. Dit getal geeft de verhouding aan van de overspanning gedeeld door de constructiehoogte. Ter vergelijking: bij een ZIP liggerdek bedraagt de slankheid 25.
Naar grotere overspanningen
Aan het eind van de jaren ’80 vormde de toevoeging van het VIP liggersysteem de afsluiting van de standaardisatieperiode 1970-1990. De geboorte van deze ligger was ingegeven door de wens nog weer grotere overspanningen te kunnen maken met relatief lichte profielen die ook nog met een grote tussenruimte werden geplaatst. Zodoende zou een brugdek per m2 een minimum aan betonvolume vragen en dat is per definitie een economische bouwmethodiek.
Het meest sprekende voorbeeld van een VIP liggerdek is natuurlijk de bouw van de Tweede Van Brienenoordbrug in de jaren 1987-1990. Bij dit markante project vormden VIP 2600 liggers de basis van de aanbruggen.
Deze balken, 2600 mm hoog en 52 m lang, werden op een onderlinge afstand van 3 meter geplaatst. Vervolgens werd een roosterconstructie gevormd dankzij vier in-situ dwarsdragers die werden voorzien van naspanning. Op dit rooster werden prefab platen gelegd waarop vervolgens een gewapende druklaag als rijdek werd gestort. Zo ontstond een dek met een constructiehoogte van 3000 mm. Het 27 m brede dek bevatte echter slechts 9 liggers die niet breder waren dan 1180 mm aan de onderflenszijde. Overigens is dit geen methode om slank te bouwen want de slankheid is slechts 16! Deze balken hadden een gewicht van 112 ton en werden per ponton van de Spanbeton fabriek in Koudekerk aan de Rijn naar de bouwplaats in Rotterdam vervoerd. Voor die tijd waren deze afmetingen en gewichten grensverleggend voor de prefabricage van bruggen en viaducten.
Zo komen we bij de laatste periode van 20 jaar: 1990 – heden. De beschikbare systemen waren in drie hoofdtypen te onderscheiden:
• een volstortligger voor kleine overspanningen, tot 15 m;
• het ZIP/VIP of railbalkensysteem met een gewapend betonnen druklaag, in het werk aan te brengen;
• het SKK kokerliggersysteem.
Deze periode wordt verder gekenmerkt door de volgende veranderingen in het bouwen in Nederland:
• de overheid treedt terug en laat ontwerpen over aan de markt, opkomst van design + construct;
• een toenemende invloed van architectuur op de vormgeving van bruggen en viaducten;
• de toename van capaciteit van transport- en montagemiddelen;
• de hinder voor het verkeer tijdens de bouw moet worden geminimaliseerd;
• er is een toenemend gebrek aan geschoolde bouwvakkers.
Recente ontwikkelingen
Het is buitengewoon interessant om te zien hoe deze veranderingen invloed hebben gehad op de ontwikkeling van prefab beton. Dit kan geïllustreerd worden aan de hand van de volgende voorbeelden.
1. Ontwikkeling en toepassing van de horizontaal gebogen kokerliggers. Deze werden voor het eerst toegepast bij de aanleg van de Ringlijn voor de metro van Amsterdam. Bij dit project had de architect, namens het GVB van Amsterdam, de volgende visie: een zo markant boven het maaiveld gelegen boogviaduct voor twee enkelvoudige metrolijnen, moet in een duidelijk herkenbare ronde vorm worden aangelegd. Hij breidde deze visie overigens uit tot alle elementaire onderdelen van de beide parallelle viaducten. Ook de enkelvoudige kolomondersteuningen waren cilindervormig en de randelementen werden in RVS boogdelen uitgevoerd. Omdat de bestaande infrastructuur een in-situ bouwmethode niet toeliet, ontstond een duidelijke wens om horizontaal gebogen geprefabriceerde liggers in een boogstraal van 235 meter te ontwikkelen. Zo werden SKK kokerliggers van ruim 40 m lang met een horizontale kromming van 800 mm ontwikkeld en toegepast. Dankzij deze ontwikkeling volgde de succesvolle toepassing van horizontaal gebogen liggers voor het verkeersknooppunt Ridderster ten zuiden van Rotterdam en de Benelux metrolijn in Rotterdam. Inmiddels zijn horizontaal gebogen liggers met boogstralen van 100 meter en zelfs slechts 60 meter in viaducten verwerkt.
2. Opschaling van de standaardbreedten van prefab liggers. Door de wens om sneller te bouwen en dus minder verkeershinder te hebben en de mogelijkheden van de toegenomen transport- en montagecapaciteiten, kon een opschaling plaatsvinden van de afmetingen van de standaard prefab liggers. De breedte van de volstortligger ging van 660 mm naar 990 mm. De breedte van de SKK kokerligger van 1180 naar 1480 mm en inmiddels brengt Spanbeton ook een ZIP ligger in de breedte van 1480 mm op de markt.
3. Toename van de overspanningslengte van met name SKK kokerliggers. De kokerligger had in de loop van de jaren ’90 zijn bijdrage aan het snel en slank bouwen van viaducten bewezen. De volgende vraag was hoe kon worden ingespeeld op de wens naar steeds toenemende overspanningslengten, juist omdat daarmee het gewicht van deze liggers de bestaande grenzen zou overschrijden. Zie ter illustratie het tabelletje dat de ontwikkeling van de lengte en het transportgewicht weergeeft.
4. Ontwikkeling Spanbeton 3P en 4P systeem. Om aan de wens van steeds grotere overspanningen tegemoet te komen, zonder een pompeus viaduct te bouwen, zocht Spanbeton oplossingen waarbij kokerliggersystemen statisch onbepaald uitgevoerd konden worden. Dit zou immers de slankheid doen toenemen. Zo ontstond het Spanbeton 3P systeem waarbij op slimme wijze de voordelen van kokerliggers zijn gecombineerd met verschillende voorspanvormen.
Vooral de toegevoegde uitwendige langsvoorspanning levert hieraan een bijdrage. Het 4P systeem verzorgt bovendien een inwendige pijlerbalk waardoor een doorgaand prefab liggerdek wordt verkregen dat alleen nog op enkele kolommen draagt.
5. Het project Westrandweg - Kunstwerk 520 met het PIQ liggersysteem. In het volgende artikel wordt aan dit project aandacht besteed. Het toont een ontwikkeling waarbij de mogelijkheden van prefab liggers in combinatie met een uitgekiende logistiek optimaal worden benut. Tevens is het een illustratie van het moderne bouwen van vandaag en morgen, onder het motto: “Bouwen is assembleren”. Dat wil zeggen dat het bouwen aan infrastructuur in de toekomst alleen nog kan plaatsvinden door in zeer korte tijd, zonder verkeershinder viaducten en bruggen te realiseren, gebaseerd op de toepassing van grote componenten die in de fabriek worden vervaardigd. Alles draait daarbij om de organisatie van logistieke processen.
jaar |
project |
lengte SKK |
Gewicht |
1993 |
Boogviaduct Ringlijn |
40 |
108 |
1996 |
Waterlandse weg |
42 |
105 |
2002 |
A5 Raasdorp |
45 |
114 |
2005 |
A12 Nootdorp |
48 |
130 |
2006 |
RW37 Twentekanaal |
50 |
135 |
2008 |
A59 Zuid Willems Vaart |
52,80 |
138 |
2009 |
A2 Marinus van Tyrus viaduct |
54,40 |
134 |
2010 |
Westrandweg Ringvaart |
61,75 |
158 |
Tot slot
Al deze ontwikkelingen zijn het antwoord op een veranderende markt, ingezet door een terugtredende overheid. De samenwerking met partners in de keten is een absolute voorwaarde geworden. Voor Spanbeton heeft dit betrekking op de samenwerking met zijn opdrachtgevers en met zijn onderaannemers voor transport, montage en voorspanning op de bouwplaats.